Understanding CAN Bus: How Your Car’s Electronics Communicate with Each Other
Ever wonder how your car sensors communicate with each other?
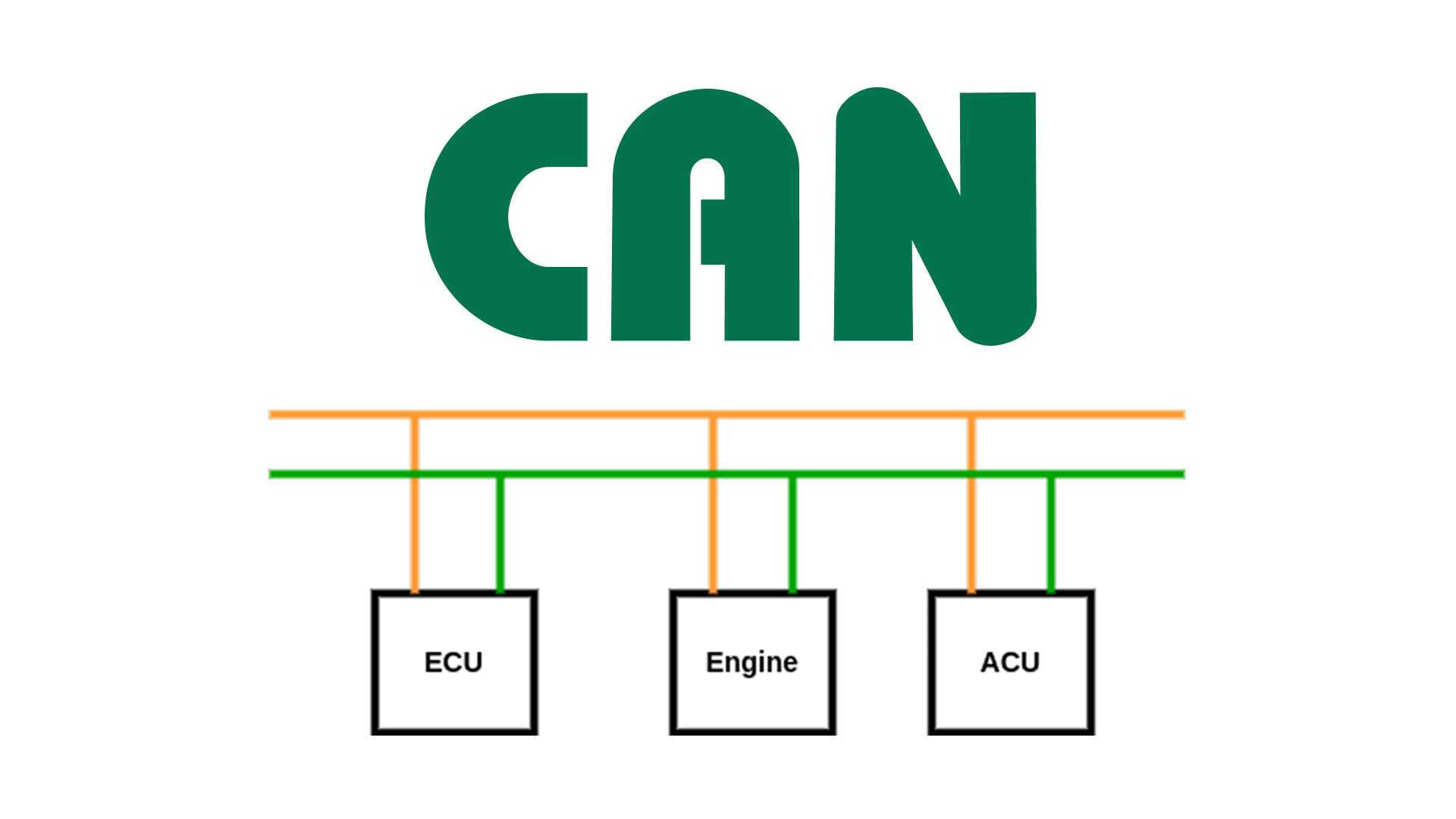
Modern vehicles are marvels of engineering, packed with multiple electronic components that work together to provide a safe, efficient, and comfortable driving experience.
From the engine and braking systems to infotainment and advanced driver assistance features (ADAS), these components constantly exchange information to ensure seamless operation.
At the heart of this intricate communication network lies a robust and reliable protocol known as the Controller Area Network (CAN).
Often described as the "nervous system" of the car, CAN facilitates the exchange of data between numerous electronic control units (ECUs) and sensors throughout the vehicle.
In this blog post, let’s understand how CAN protocols are implemented in automotive systems.
What is CAN?
The CAN protocol was initially conceived and developed by Robert Bosch GmbH in the early 1980s.
Its primary motivation was to address the increasing complexity of wiring harnesses in automobiles.
Before the advent of CAN, each electronic device in a vehicle typically required a dedicated point-to-point wiring connection to communicate with other components.
As the number of electronic features in cars grew, this resulted in a tangled and cumbersome mass of wires — increasing vehicle weight, cost, and the potential for failure.
Recognizing these limitations, Bosch developed CAN as a more streamlined and efficient communication solution.
The protocol was later standardized as ISO, solidifying its position as a key technology in the automotive sector and beyond.
Key Advantages of CAN
The widespread adoption of the CAN protocol in the automotive industry can be attributed to its numerous inherent advantages.
One of the most significant benefits is its high reliability.
CAN is designed to be robust and fault-tolerant, making it suitable for use in critical systems such as engine control and braking.
The protocol incorporates built-in error detection and handling mechanisms to ensure data integrity.
Furthermore, CAN offers a low-cost communication solution.
Its simple and efficient signaling method allows for cost-effective implementation — particularly important in the price-sensitive automotive market.
By utilizing a shared two-wire bus, CAN significantly reduces the amount of wiring and copper needed in a vehicle, leading to lower weight and minimal wiring.
This reduction in wiring not only lowers manufacturing costs but also contributes to improved fuel efficiency due to the decreased vehicle weight.
The CAN protocol also demonstrates excellent scalability, capable of supporting a large number of devices (or nodes) on a single network.
This makes it easy to add or remove electronic components as needed without major modifications to the existing communication infrastructure.
Another key feature is its multi-master capability.
Unlike older communication protocols that rely on a central master device to control all communication, any nodes on a CAN network can initiate communication when the bus is free.
This distributed control architecture enhances the system's flexibility and resilience, as the failure of one nodes does not necessarily halt communication across the entire network.
How the CAN Protocol Enables Emergency Responses
Imagine your car’s electronic parts as friends in a chat group.
When one friend has important news, they send a message that everyone sees right away.
Here’s how it works during a crash:
-
Sensing the Crash and Popping the Airbags
-
Tiny crash sensors feel a sudden, hard jolt.
-
They immediately send a “Crash happened!” alert on the shared wire (the “chat group”).
Because this alert is tagged as very urgent, it gets sent first. -
The Airbag Control Unit (the friend who watches for crash alerts) reads that message.
-
If the message says the bump is big enough, it commands the airbags to inflate — in just a few milliseconds.
-
-
Notifying Other Systems
- The same “Crash happened!” alert is also seen by other control units, like the main engine computer or the Telematics Control Unit (the friend who makes calls.
They’re all listening for that exact alert, so they know something serious just occurred.
- The same “Crash happened!” alert is also seen by other control units, like the main engine computer or the Telematics Control Unit (the friend who makes calls.
-
Making the Emergency Call
-
The Telematics Control Unit (TCU) sees the crash alert and decides to call for help.
-
To tell responders where you are, the TCU asks the GPS module (another friend in the group) for the car’s location.
-
It sends a “Where are we?” message.
-
The GPS module replies with the latitude and longitude.
-
Now armed with crash and location data, the TCU uses its built-in phone to dial the emergency number.
-
It reads out, “Crash detected. This is our location: coordinates.”
-
In simple terms, the CAN bus is like a super-fast group chat inside your car.
One sensor’s urgent message goes out to everyone at once, so each part — airbags, engine computer, emergency caller — can do its job right away without messy, separate wiring.
How CAN Communication Works
Understanding how CAN physically transmits data is key to appreciating its robustness:
-
CAN uses a simple two-wire bus, typically labeled CAN High (CANH) and CAN Low (CANL).
-
Data is sent using differential signaling, relying on the volatage difference between CANH and CANL, rather than absolute volatage levels. This makes it highly resistant to electrical noise.
-
The protocol defines two states:
-
Dominant (logic '0'): CANH is high and CANL is low, creating a volatage difference (around 2V).
-
Recessive (logic '1'): both lines are near the same volatage, representing the idle state.
-
-
Recessive are generally used for the bus wiring to help cancel out interference.
-
Termination resistors (typically 120 Ohms) are required at each end of the bus to prevent signal reflections that can disrupt communication.
-
Different CAN speed variants exist:
-
High-Speed CAN (ISO 11898-2) (up to 1 Mbit/s) for critical, real-time applications (ABS, Engine Control).
-
Low-Speed/Fault-Tolerant CAN (ISO 11898-3) (up to 125 kbit/s) for less time-sensitive systems (power windows, diagnostics).
-
CAN FD (Flexible Data Rate) (up to 8 Mbit/s) offers higher speeds and larger data payloads for modern, data-intensive features.
-
The use of differential signaling and termination is crucial for CAN's reliable performance in the electrically noisy automotive environment.
These key physical-layer features ensure that CAN remains a robust, scalable, and cost-effective backbone for in-vehicle communications.
CAN Speed Variants
You can refer to the following table to summarize the key differences among the major CAN variants:
CAN Type | Speed (max) | Typical Automotive Applications |
---|---|---|
High-Speed CAN (ISO 11898-2) | 1 Mbit/s | ABS, Engine Control, Airbags, Electronic Stability Control (ESC), Powertrain Control (PCM) |
Low-Speed/Fault-Tolerant CAN (ISO 11898-3) | 125 kbit/s | Power Windows, Door Control, Light Control, Diagnostics, Dashboard Controls and Displays, GPS, Radio |
CAN FD (Flexible Data Rate) | Up to 8 Mbit/s | Advanced Driver Assistance Systems (ADAS), High-bandwidth Sensor Data, Infotainment |
Conclusion
In conclusion, the Controller Area Network (CAN) protocol stands as a cornerstone of modern automotive electronics.
Its inherent reliability, efficiency, and cost-effectiveness have made it the go-to solution for enabling seamless communication between the multitude of electronic systems within a vehicle.
While newer and faster communication technologies are emerging to address the ever-increasing demands of automotive innovation, the fundamental principles and robust design of CAN ensure its continued relevance for the foreseeable future.
The ongoing evolution of the protocol, with the introduction of CAN FD and other advancements, further demonstrates its adaptability and capacity to meet the evolving needs of vehicle electronics.
As vehicles become increasingly complex and interconnected, the CAN protocol will undoubtedly continue to play a vital role in powering the driving experience for years to come.
LiveAPI: Interactive API Docs that Convert
Static API docs often lose the customer's attention before they try your APIs. With LiveAPI, developers can instantly try your APIs right from the browser, capturing their attention within the first 30 seconds.